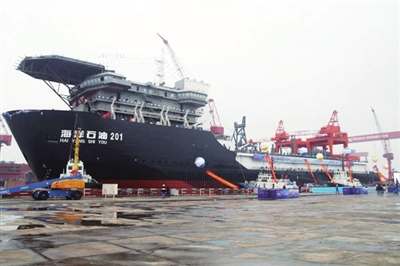
2012年5月15日,由中国
海洋石油总公司与中国熔盛重工集团控股有限公司共同打造的我国首艘深水铺管起重船“海洋石油201”在山东青岛海洋石油工程 有限公司码头隆重举行建造竣工和启航仪式,标志着这一具有世界先进水平的深海开发重大装备历经一系列码头试验和两次全面试航验证已成功建成。该船将启航开 赴南海投入试铺管作业和荔湾3-1气田1500米深水铺管施工作业,这也是继5月9日“
海洋石油981”成功开钻后我国海洋石油工业“深水战略”取得的又 一实质性成果。
与“海洋石油981”主要用于南海深水油气田的钻井、
完井和修井作业不同,“海洋石油201”承担着深水油气田海上生产设施建设的重任,能够从事固定式、浮式和水下油气生产设施安装以及海底管道铺设等全方位海上施工作业。该船设计、建造和施工关键技术攻关被列入“
十一五”期间国家科技重大专项和国家重点“863”项目,是高科技发展规划的重点项目。该船的成功建造和投用,填补了中国在深水工程建设特大型装备项目上的空白。
“海洋石油201”是世界上第一艘同时具备3000米级深水铺管能力、4000吨级重型起重能力和DP-3级动力定位能力的船型深水铺管起重船,能在除北极外的全球无限航区作业;集成创新了多项世界顶级装备技术,并融入中国海油的需求和设计理念,配置了包括全电力推进、全电力变频驱动、DP-3动力定位、深水“S”型双节点铺管系统、4000吨重型
海洋工程起重机等一系列国际上最先进的技术和装备,是亚洲和中国首艘具备3000米级深水作业能力的海洋工程船舶;入中国船级社(CCS)和美国船级社(
ABS)双船级,其总体技术水平和综合作业能力在国际同类工程船舶中处于领先地位。
“海洋石油201”船长204.65米,型宽39.2米,型深14米,独特的双层甲板面积超过两个标准足球场面积;安装深水托管架后船长约280米,主起重机作业时从船底到主起重机顶高度达136.77米,相当于45层楼高;定员达380人,是中国海洋石油大型装备和设施中定员最多的;续航能力达12000海里,自持力达60天;全船管道系统长度超过70公里,电缆长度超过800公里,设备多达4247台套,I/O点超过12000点,结构用钢超过18000吨;船舶自重达34832吨,排水量达59101吨,甲板可变载荷达9000吨。
深水铺管起重船“海洋石油201”,是中国海油与熔盛重工首度合作的海洋工程项目,由中国海油控股的海洋石油工程股份有限公司全额投资建造和负责运营。项目于2005年5月启动,2008年9月16日开工建造,2012年4月28日海油工程与熔盛重工签署“交船确认书”。
大型深水装备是“流动的国土”,是大力推进海洋石油工业跨越发展的“战略利器”,“海洋石油201”启航南海投入我国的第一个深水油气田——荔湾3-1气田的1500米深水铺管作业,必将载入中国海洋石油工程建设的史册,开启中国海油正式挺进深水的新征程。与“海洋石油981”等“深水舰队”成员一起配套使用,使中国成为第一个在南海自营
勘探开发深水油气资源的国家。拥有独立深水
油气勘探开发能力,对有效开发南海深水油气资源具有非常重要的意义,也为与周边国家合作勘探开发深水油气提供了坚实的技术和装备基础。
【小百科】“海洋石油201”的9个世界首次
1、首次采用集专业S型
铺管船高效作业所需的良好船舶运动性能和4000吨级以上大型起重船安全作业所需的良好船舶稳性于一身的优化船型设计,实现安全可靠的和高效的作业。
2、首次针对我国南海和东海开阔海域波浪特征设定船舶固有横摇周期用于船型设计,大幅度提升了船舶的运动性能和可作业率。
3、首次在大型起重船的基础上实现深水三套三型铺管系统的总体设计,满足各类深海开发项目的施工作业需要。
4、首次实现深水S型双节点铺管系统和大型起重机系统在船舶的同时布置,解决了众多复杂系统在狭长船体上的布置难题
5、首次研制出集吊、送、运一体的全电力变频驱动多功能管子装卸机,提高了作业效率,节省了甲板空间,降低了噪音,实现了低碳排放。
6、首次采用折叠式钢架后背绳艉固定设计的4000吨主起重机,大幅提高模式转换的作业效率,以较低成本大幅提升起重能力,是世界上设计工况要求最高的重载轻型海洋起重机。
7、首次同时采用最新技术的深水铺管作业动力定位模式(动力定位系统深水铺管模式与张紧器和弃管回收绞车系统深水模式匹配)和高精度起重作业动力定位模式,有效提高不同作业的动力定位精度、作业效率和作业安全。
8、首次对全船作业设备和推进系统全部采用电力变频驱动技术,全面实现节能减排降噪目标;通过谐波分析和系统配置研究,解决了船舶电网稳定的技术难题。
9、首次采用DP-3+DP-2动力定位的组合性能,实现更大程度的冗余,满足不同作业工况要求;通过复杂的功率管理系统逻辑控制关系,解决了单线母排设计方案满足DP-3+DP-2要求的技术难题,有效节约成本。