简介:委内瑞拉国家石油公司拥有开采重油的专业技术,几年来在委内瑞拉东部油田开采出了几百万桶重油。经过现场应用效果,该公司采用不使用稀释液的冷采方法,并判定最经济的举升方法是使用螺杆泵。
Heavy lifting solved in Venezuela
Faced with trying to produce 8.6°API crude with viscosity beyond 10,000 cP, PdVSA found innovative solutions to lifting and metering problems.
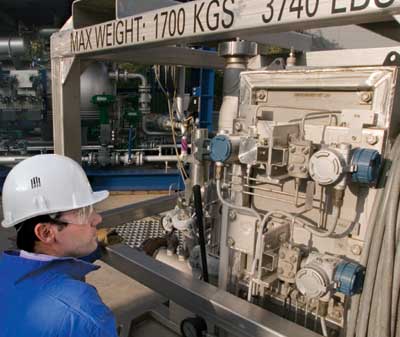
The PhaseTester portable multiphase flowmeter with Vx technology is skid-mounted for easy setup on location. (Images courtesy of Schlumberger)
Venezuela has undertaken an aggressive policy to improve its overall petroleum production. Experts are making the country’s fields, including those containing heavy oil, produce early and efficiently.
Petróleos de Venezuela S.A. (PdVSA) has expertise in heavy oil production, having developed and produced millions of barrels from the eastern Venezuela oil fields over the years. Today, the company is putting its experience to work in challenging new areas.
Producing Orocual
Recently, the company began producing extra-heavy oil from a cluster of wells in the Orocual field in the northern part of Monagas State just north of the city of Maturin. Discovered in 1933, Orocual lies at the northeast tip of the Jusepin complex, but unlike oil at Jusepin, Orocual crudes can be heavy. Gravity ranges from 8.6°API to 10.6°API with viscosity at line conditions beyond 10,000 cP. Wells in Orocual produce a wide range of fluids from heavy and extra-heavy crude to gas condensates, to light and medium oil. The main reservoir is the Pliocene Las Piedras formation, which produces from sandstones between 2,000 and 8,000 ft (610 and 2,439 m).
Over the years, the company has tried diluents, steam, and other methods of reducing oil viscosity to stimulate production from its heavy oil areas. These worked, but proved to be costly and took a long time to implement, particularly when the technologies were applied across an entire field.
In a search for a better solution, PdVSA authorized a small early production facility project to see if it could better produce heavy oil. After considering several alternatives, the company chose to employ cold production methods without diluents. The most economical lifting method was determined to be progressive cavity pumps.
The first challenge was to measure production. Traditional methods using separators proved problematic. Much of the crude is produced as foam, which leads conventional separation methods to be ineffective. Liquid flow rates could not be measured with any consistency, and because gas was being vented, no gas measurements were possible. Since the project was a new development, there was no historical data from which to work. To meet PdVSA’s production objectives, it would be necessary to get an accurate production measurement and to provide access to both total flow rate and gas volume fraction data.
For several years, Schlumberger has been working to extend its capability to accurately measure heavy crude production. Prior to this project in Venezuela, the lowest gravity measured had been 13°API. Through dedicated heavy oil programs and experience in less viscous fluid (<5,500 cP) around the world, experts believed they could adapt the PhaseTester portable multiphase flowmeter to this job.
The biggest advantage of the multiphase flowmeter is its ability to measure individual phase fraction flow rates without separation. The meter accomplishes this by employing a nuclear mass attenuation principle that distinguishes fluids by composition rather than density.
The meter can differentiate among oil, water, and gas by measuring their phase holdups.
The equipment uses Vx multiphase well testing technology, based on a specific-fraction high-frequency measurement technique, to enable accurate multiphase flow measurements. The meter is unaffected by foams and emulsions that are typical in heavy oil environments. The equipment had not been used before this application to measure crude as heavy as that produced in the Orocual field or for viscous fluid beyond 10,000 cP at line conditions.
Adapted to meet the challenge
Efforts to extend the operating envelope of Vx technology in the field led to the creation of special procedures that have resulted in greater accuracy through a refined interpretation model.
Procedures include a fit-for-purpose fluid properties package, which avoids the additional cost and complication of installing a heater upstream of the PhaseTester equipment, generally required to lower viscosity.
Since typical interpretation is based on a series of well-known correlations from an extensive database, it was necessary to expand the operating envelope of the interpretation package. This was done by removing some of the unknowns. Using the pressure-volume-temperature (PVT) Express onsite well fluid analysis service to zero in on the fluid properties through improved understanding of the fluid’s composition, enough uncertainties were removed to permit a robust flow analysis.
Fluid analysis requires a sample of less than 1.7 fl oz (50 cu m) of reservoir fluid collected from downhole or surface. Results are available quickly and can be downloaded directly into the multiphase flowmeter to obtain highly accurate viscosity measurement and flow rates. Oil shrinkage was greater than 50% with this fluid, a parameter that could not have been estimated correctly by a standard PVT package.
Adaptations enabled measurement of extremely low gas rates and resolution of liquids with low density contrasts. The resulting measurements are more accurate than those from a traditional separator and are delivered in real time.
The addition of an accurate gas production rate proved valuable to PdVSA. The cumulative gas rate from all four wells of the pilot program averaged slightly more than 400,000 cf/d. Crude oil rates presented in real time compared favorably with those acquired using a stock tank measurement with all its associated lengthy delays.
Multiphase flowmeters cut field development costs
Among the many benefits of multiphase flowmeters are improved reservoir characterizations, in a fraction of the time required by traditional methods. Speed has enabled a marked improvement in well diagnostics, including early detection of water or gas coning. And from a logistics standpoint, eliminating test lines, test separators, and gas venting has enhanced safety and improved environmental compliance.
So how does it work? The equipment controls the environment by forcing flow through a calibrated Venturi measurement chamber where a high-speed multi-energy gamma ray holdup meter makes accurate and repeatable phase fraction flow measurements with little or no stabilization time requirement. The equipment is configured to impose a specific flow-shape factor on the production stream, eliminating the effects of slug flow, foam, or emulsion environments. The system requires no process control because it is insensitive to changes in flow rate, phase holdup, continuous phase flow or pressure regime. No moving parts are required.
Problems solved
Deploying the multiphase flowmeter, in addition to providing accurate phase flow rates, has helped PdVSA solve additional problems. At Orocual, engineers wanted to know how fast they could pump wells without damaging the formation at the completion. Once they were satisfied that the flowmeter could answer macro field production questions, they asked to use the equipment to measure flow rates from individual wells.
In addition to answering the formation damage question, PdVSA engineers were able to identify problem producers. Adapting multiphase technology in extra heavy oil and high viscosity and extending it to a much lower production range averaging 50 b/d, led to a new challenging problem for individual wells where production was intermittent.
This was handled by putting proper averaging techniques in place and adequate viscosity inputs at line conditions.
If heavy oil production can be measured consistently and accurately enough to routinely produce crude without using diluents or steam, it will be an economic breakthrough that will have far-reaching benefits.