简介:主要介绍壳牌等公司钻机设计、控制压力钻井、套管钻井、小井眼智能马达等新的钻井技术。
Drilling technology breaks new ground
Drilling technology adds value to oil and gas reserves in 2008.
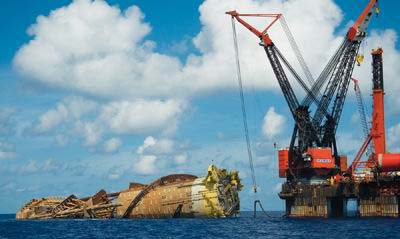
Expected to be online in 2010, Shell’s Perdido spar will hold multiple world records as the deepest oil development and the deepest drilling and production platform. It will also have the deepest subsea well in the world. (Image courtesy of Shell)
The drilling industry proved many new technologies in 2008, with remote and hard-to-reach resources influencing equipment design. Combined, new technology and equipment are reducing costs and lowering risk by bringing resources to the surface faster.
Rig design
Rowan Companies recently completed its first of four newbuild jackups in November. The new 240-C jackup design is outfitted for a class above the company’s 116-C and Tarzan rigs, offering more deck space in the same footprint. The design is geared for use in the deeper water of the Gulf of Mexico (GoM), southern and central North Sea, and the shallow waters of the Scotian shelf. The rigs also are being marketed for extended-reach drilling projects and ultra-deep drilling. These jackups can operate to 400 ft (122 m) water depth and have drilling capacity of 35,000 ft (10,675 m).
Rowan’s 116-C, long considered the “workhorse” of the offshore industry, has had a good run, but Rowan’s new rigs are more robust than their predecessors and are designed for high performance in harsh environments. Following the deput of the first 240-C in November, three more are planned for construction.
Shell’s Perdido spar, designed as a combination drilling/production platform, moved into place 200 miles (322 km) off the Texas coast in August 2008. The spar was installed in the ultra-deep region of the GoM in about 8,000 ft (2,440 m) of water. It will hold multiple world records as the deepest oil development and the deepest drilling and production platform. It will also have the deepest subsea well in the world.
Dale Snyder, project manager, said the purpose-built spar was designed to provide drilling capacity without waiting for a semisubmersible rig for every project. The Noble Clyde Boudreaux was used prior to the spar’s installation to back-set (7,000 ft) the top sections of 22 wells. The Perdido spar will use wet-tree direct vertical access (DVA) wells, which incorporate a surface blowout preventer (BOP) for drilling/completion of subsea wells to remove weight from the platform. The surface BOP system will allow the spar to drill, complete, and intervene on wells directly underneath. The production and drilling platform is expected to be completed in 2010 and will produce an estimated 100,000 b/d of oil and 200 MMcf/d of gas.
Managed pressure drilling
Managed pressure drilling (MPD) allows drillers to control the annular pressure profile throughout the well bore. The goal is to determine the downhole pressure environment limits and to manage the annular hydraulic pressure profile accordingly. By controlling the annular pressure profile, a well can be balanced at all times. The technique is an enhanced form of well control that allows drillers to manage unexpected pressures.
MPD technology is particularly advantageous in maturing fields like those in the North Sea. National Oilwell Varco’s (NOV’s) continuous circulation system (CCS) provides reduced risk of lost circulation; formation fracturing; kicks; differential sticking; stuck bits or bottomhole assemblies; easier navigation of narrow pore pressure or frac pressure gaps; longer drilled sections prior to casing; longer laterals because of continuous cuttings transport; steady density, temperature, and flow of returning mud and cuttings; and easier dual-density drilling. Safety also is increased because connection kicks are avoided.
Steady downhole pressure is provided by enclosing the tool joint to be disconnected in a pressure chamber, which allows drilling fluid to flow down the drillstring as the CCS disconnects the tool joint. The upper tubular is withdrawn, and a set of blind rams separates the CCS into two chambers. The upper chamber is depressurized, which allows the top drive sub to withdraw and acquire a new tubular. The new tubular is inserted, brought up to pressure, and connected to the drillstring while drilling-fluid flow down the drillstring remains steady.
Casing drilling
Strides were made by Weatherford this year with the Drilling-with-Casing (DwC) service, which was used to batch-drill 10 wells with 13 3⁄8-in. surface casing at the Zhuang Hai-4 area of Dagang field. The Dagang Oil Field Shallow Water Co. division of PetroChina used DwC technology to save US $320,000 at the completion of the project, according to Scott Beattie, global business leader for DwC with Weatherford.
Although this job involved batch drilling the top-hole section, the system reduces risk in many jobs. From that viewpoint, drilling with casing eliminates problems with lost-circulation zones, depleted reservoir sections and unstable formations.
Improved logging
One of the most interesting innovations in logging in 2008 was Impact Guidance Systems’ DataCoil, a new memory-based coiled tubing (CT) logging tool that can measure temperatures up to 300°F (150ºC) and pressures of up to 10,000 psi, both internally and externally to the coil.
DataCoil records compression and tensile forces for use in applications where CT drilling on plugs, packers, etc. can benefit from this data. Inclination of the well bore is also recorded, which has provided critical data when entering multilaterals. The tool also records mechanical and hydraulic impact forces on the bottomhole assembly (BHA). Designed with a true bi-directional sensor, the tool delineates upward impacts from any recoil in the string affected by the impact force with a sensitivity ranging from 200-150,000 lbs.
Following the tool’s continued use in more than a dozen projects in Alaska and the GoM, a real-time version was recently developed (jointly with a US operator) and is currently being commercialized.
Through-the-bit logging technology, newly developed by ThruBit LLC, offers an alternative to standard openhole wireline conveyance and logging while drilling. The ThruBit Logging system uses small-diameter logging tools conveyed through the drillstring and BHA.
The tools are designed to pass through a specially designed PDC bit known as the Portal Bit, which is modified with a removable central section. Formation evaluation data is acquired with either wireline or memory tools, in the latter case while tripping drillpipe out of the well, thus improving rig efficiency.
Slimhole smart motors
Horizontal directional drilling reduces environmental impact and improves recovery, particularly in coalbed methane (CBM), unconventional shale, and tight gas horizontal drilling. Scientific Drilling’s Smart Motor is improving success for drilled laterals and multi-laterals in both thick and very thin coal seams as narrow as 2 ft (.6 m).
The tool uses emerging navigation technology designed specifically for lateral wellbore placement. The Smart Motor contains a power section, a smart housing containing the sensors, a bent housing, and a bearing section. The sensors are placed on the motor above the bend, which allows more accurate inclination readings and protects the sensors from extreme downhole conditions.
Until now, this specialized equipment was not available in a size that could be used to drill a 43⁄4-in. wellbore. A 33⁄4-in. Smart Motor was tested in June 2008, however, and the results of the field trials have been extremely successful.
With the Smart Motor, operators can now drill 3,000 ft (915 m) horizontally into the coal seam in 24 hours ? a dramatic decrease in drilling time. Recently, Mountaineer, with a Scientific Drilling crew, drilled a horizontal CBM well in less than eight days. This technology also opens up narrower seams for drilling, which increases access to reserves.