简介:Teledrill公司最近推出其脉冲钻井新技术,与常规钻井技术相比,它能将机械钻速提高50%至400%之间,并能同时进行随钻测量。
With a promise of putting the power of the pumps at the drill bit, Texas-based Teledrill has recently unveiled its new pulser drilling technology. The tool, also called the Teledrill, provides a significant increase in the rate of penetration (ROP) compared to conventional drilling technology and simultaneous measurement-while-drilling (MWD) in one compact, downhole tool.
.JPG)
The original concept of the Teledrill tool was to create a simple, yet technically advanced, alternative to existing MWD technology, according to Dave Kusko, Founder and Vice President of Teledrill. “We soon realized that we could enhance ROP while providing MWD services in one unique tool. This ROP enhancement has varied from a 50% to a 400% increase in ROP.”
Pulsing provides ROP advantage
The ROP advantage results from the Teledrill tool’s ability to harness the power of the drilling-fluid pumps at the drill bit. The tool incorporates a pulser component that opens and closes to deliver a hammer-drill-like force through the bit. This force breaks up the formation. Having the power distributed at the bit results in a “picking action” which according to preliminary tests allows the Teledrill to produce a straighter hole.
The amplitude of the jarring force can be as high as 15,000 lbf with a minimum power requirement of approximately 20 W. It is unleashed through the bit when the pulser closes. When it opens, the pulser lifts and cleans the bit by releasing the pent up energy in the fluid column.
Kusko explains that this mode of operation differs from a hammer drill in that the Teledrill does not rely on solid-on-solid contact to generate the extreme jarring forces. The internals of the Teledrill are immersed in the drilling fluid. The pulse is created when the Teledrill stops the flow of the drilling fluid and then quickly releases it. “The tool provides a pulsing force with amplitudes ranging from 10 to 15,000 lbf, with larger pulse amplitudes providing higher ROP,” he added.
.jpg)
The company has performed a series of well tests on turnkey drillers’ rigs, using both roller cone and PDC bits. In certain lithologies, Teledrill has demonstrated the tool’s ability to triple ROP compared to conventional drilling technology. “While field testing in our first six wells, we never drilled a 30-foot stand in less than 50 feet per hour. We also ran tests where pulsing was activated and then deactivated. Pulsing made a significant difference… On average, the Teledrill ROP was 115 to 120 feet per hour. Without pulsing, the ROP average dropped to approximately 40 feet per hour on the same wells.”
This enhancement in ROP has economic benefits to operators facing high rental rates for drilling equipment. “Increased drilling rates translate to subsequent decreases in rig tool rental costs and drilling personnel costs,” said Kusko. “We have calculated that reduced drilling time can create a 40 percent reduction in drilling costs when we’re in the hole.”
“For example, if an E&P company paying USD 18,000 per day to rent a rig experiences a 100% ROP increase with the Teledrill, they could save USD 2.3 million per year per rig in rental expenses alone, assuming it operates for 250 days per year,” he continued.
The tool contains its own turbine generator, which is activated by the drilling fluid flowing around it. This turbine allows Teledrill to stay downhole for longer periods, and in the event that the drilling fluid stops and turbine power is lost, primary or rechargeable backup batteries provide power to the system. Teledrill believes they have the only retrievable turbine generator in a downhole MWD tool.
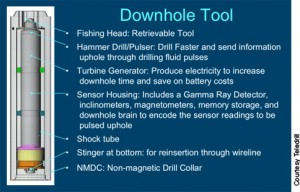
Suite of real-time sensors guides accurate drilling
Located in close proximity to the pulser is Teledrill’s sensor housing, which contains a suite of MWD sensors. Teledrill’s inclinometers measure inclinations downhole and send surveys uphole through large magnitude pulses. These pulses can be counted on an analog weight indicator to determine downhole inclination without decoding software, pressure transducer or engineer. This information is also sent uphole through positive mud pulse telemetry in typical MWD form. A gamma ray detector is included in the sensor package, which allows the operator’s team to steer the bit and remain in the zone of interest. The Teledrill also has magnetometers and a downhole computer. The computer encodes all sensor readings into telemetry that is pulsed uphole in real time and saves the readings to memory for downloading on the surface.
Kusko states that the Teledrill package is extremely compact at 10 to 13 feet in length. This makes it approximately one-third the length of MWD-only tools. “All components are housed in a nonmagnetic drill collar, which includes an integral shock dampening housing to enhance tool reliability,” he said. “The tool was designed for simple transport and assembly in the field, and all components?the drill collar, rig equipment, and downhole tool?fit into a short trailer, something that is not possible with conventional 30-foot drill collars.”
The entire tool is easily retrievable from the well in the event that adjustments are necessary. “The Teledrill can be retrieved with slickline and a 1.5-in. pulling tool through an inner diameter of greater than 1.75 in.,” Kusko said. He added that the company has never failed to retrieve the tool unless there has been some sort of downhole failure or restrictions in the BHA.
A recent field test demonstrated the robustness of the tool. “We recently ran the Teledrill in a poorly conditioned well that contained a great deal of sand and minimal filtration, really a pretty erosive operating environment,” said Kusko. “After 72 hours under these conditions, the tool was still working. We really don’t know the upper limit on reliable operating time in cleaner well environments, because so far only one well test was run with conditioned drilling fluid.”
Other features include greater power distribution at the bit and a jarring action which should reduce the common problem of stick-slip in horizontal wells. This technology should hypothetically increase the length of horizontal and vertical drilling.