简介:海低油气分离,液体助推是一种有效的油藏开发技术。从最近的几个案例来看,如Pazflor、BC-10以及Perdido,与单纯进行提升相比,利用新方法可以大大提高采收率,而成本增加微乎其微。
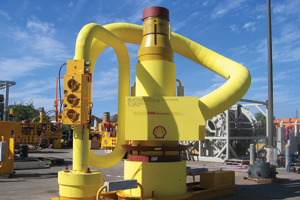
In subsea environments, near-well installation of multiphase pumps has been a proven approach to achieving improved asset values and increased production. Yet while use of multiphase pumps is in many instances an effective solution, special consideration as to approach must be taken when challenging conditions exist such as are found in deeper water or with long tieback distances, or when heavy-oil production is involved.
Despite advances, multiphase pumping technology remains limited in its capabilities. Dynamic ? i.e., centrifugal and helico-axial ? pumps function with reasonable efficiency for single-phase, low-viscosity liquids. However, they become very inefficient when a high-viscosity liquid is combined with high percentages of free gas.
More effective oil reservoir exploitation can be achieved using subsea separation coupled with liquid boosting. This approach enables production at very low flowing tubing head pressure, around 500 psi, even when water depth approaches 10,000 ft (3,000 m) and step-out distance from the host exceeds 30 miles (48 km).
This method also is well suited for use where heavy oil or low-reservoir pressure is the rule. And it is especially effective when combined with gas-lift of the production wells.
Examples from several recent projects ? including Pazflor, BC-10, and Perdido ? demonstrate that gas-liquid separation prior to liquid boosting improves recovery considerably more than boosting alone, while adding only limited incremental technical costs. Single-phase pumping facilitated by gas-liquid separation delivers the performance needed to exploit a reservoir’s full potential, while providing enhanced flow-assurance capabilities.
What’s gone before
To date, the most commonly accepted method for improved subsea processing has been installation of a multiphase pump close to the well. These pumps have operated successfully for several years. Yet use has been limited to shallow-water and shorter tieback distance environments.
This is primarily due to pumping-technology limitations. To date, multiphase pump projects have been restricted to those requiring up to 700 psi of incremental drawdown. Deep water or long tiebacks require much higher pressures.
A “rule of thumb” can be applied to help understand how much pressure a pump might need to deliver as depth and distance increase: Take the water depth (in feet) and multiply by a typical multiphase gradient (0.3 psi/ft); plus the tieback distance (miles); and multiplied by a typical multiphase pipeline frictional loss (50 psi/mile).
Thus, for a reservoir in 6,000 ft (1,830 m) of water, located 15 miles (24 km) from a potential host, the water depth contributes 6,000*0.3=1,800 psi, while the step-out contributes 15*50=750 psi, for a total potential pump duty of 2,350 psi. Assuming pump-suction pressure equals fluid-boarding pressure, this value is equivalent to the required pump duty.
In reality, typical multiphase pump projects have operated with minimum suction pressures in the 1,000 to 1,500 psia range, with typical boarding pressures of around 250 psia. This is because a suction pressure of 500 psia could easily result in a free-gas volume above 85% for many Gulf of Mexico Miocene oils. The actual free-gas percentage is affected by the production gas-oil ratio, which itself is a function of any gas-cap production and the oil’s bubble point at suction conditions. Available head and hydraulic efficiency are poor for dynamic pumps under these circumstances.
While oil containing even higher free-gas levels can be processed, there will be a corresponding reduction in hydraulic efficiency and head. Operations involving gas-lift in the production wells ensure that multiphase pumping is found inadequate. Single-phase pumping facilitated by subsea gas-liquid separation will in many cases realize the potential of gas-lift.
Recent work with single-phase subsea, multistage centrifugal pumps has shown that 4,000 psi is possible with low-viscosity (<1 cP) liquids. Even this upper limit could be exceeded once subsea motor technology catches up with the pumping capabilities. Dynamic pumps can be applied in situations where the liquid viscosity exceeds ~100 cP at inlet conditions, but their ability to generate head is thereby somewhat compromised ? and severely compromised when free gas is added to the equation.
Finally, with hydrate management being one of the most crucial production areas to address, the separator also allows field operation outside the hydrate formation region.
Case use examples
To better understand a separator’s impact, three current projects using gas-liquid separation and liquid boosting will be examined.
For these recent projects ? BC-10, Pazlor, and Perdido ? the hydrate management philosophy is broadly the same. Venting of pressure at both ends of the pipeline enables the pressure to be safely reduced to outside the hydrate envelope.
In addition, oil that has been flashed at 500 psia in a subsea separator will have a new bubble point. This low bubble point means there is very little free gas, even under venting, thereby minimizing the possibility to form hydrates. This, plus the ability to vent from both ends of the pipeline, could give enough confidence regarding hydrate formation and remediation to forego other hydrate management technologies.
Other flow assurance concerns such as liquid slugging are also mitigated and it should be noted that where wax may be an issue, round-trip pigging through the gas line and back through the liquid line is still possible.
While all three projects use gas-liquid separation to achieve higher subsea reservoir recovery, two different separator types are used. The BC-10 and Perdido separators are identical and based on a caisson separator design. In these projects, multiphase fluids are conditioned in the inlet piping and enter the inlet block at a downward angle and at a tangent.
As a result, liquid disengages from the gas and swirls down the inside diameter of the caisson. The tangential velocity keeps the liquid from re-entraining in the gas traveling upward. There is approximately 100 ft (30 m) between the inlet nozzle and the normal liquid level. This provides upwards of 100 bbl (16 cu m) of liquid slug capacity. Just above the inlet is a gas polishing section with 32-in. inside diameter. With the gas levels envisaged for these two projects, this results in a relatively low K factor.
On the other hand, the Pazflor project uses a separator based on classic gas-scrubber design principles. In this case, the separator was made as large as possible. Here again there is approximately 20-ft (6-m) distance between the normal liquid level and the inlet nozzle is significant and provides excellent liquid slug handling capacity (75 bbl or 12 cu m). An inlet device coupled to sloping trays and troughs gives extremely good separation performance. These internals have been tested and qualified for sudden sand production levels of 10 wt% and have been shown not to clog.
For the two design types ? caisson separator and gas scrubber ? process-control sensors and liquid hold-up time deliver slightly differing performance. The caisson system in BC-10 and Perdido clocks three minutes of hold up, while the Pazflor design at maximum rate offers marginally less.
At BC-10 and Perdido, level control is calculated by differences in pressure vertically up the caisson. Although the level location can be +/- 10 ft (3 m), height changes are readily seen and the pump reacts quickly enough to maintain control. Control-system testing under transient flow and with signal delays has proven this concept. The Pazflor vessel will use a density profiler similar to that used in the Tordis project. Obviously, with less hold up, the system will have to react quickly. For this reason, Pazflor will use fiber-optic lines to carry sensor and control information to and from the host.
Final words
Subsea separation is one of the most innovative technologies being applied in the oil and gas industry today. The need exists to maximize recovery; increase pressure and hydrocarbon output at fields with low reservoir pressures; address hydrate formation risks; and reduce constraints on topside facilities.
Initial production treating at the seabed facilitates more effective exploitation of an oil reservoir. Most important, it leads to higher recoveries from subsea reservoirs.
Gas-liquid separation and liquid-boosting projects are being implemented globally as a performance solution where capabilities for traditional multiphase pumping are limited.
Application of this technology to reservoirs that can benefit from production-well gas-lift is also expected. Improved recovery, obtained with limited incremental cost, has been the means to justify gas-liquid separation and liquid boosting projects. Additional projects will follow as separator designs become smaller and technology qualification standardized.