简介:连续油管技术的发展已今非昔比,而新的管件连接处理技术要求抗疲劳寿命更长久。Global Tubing公司开发的摩擦棒焊接工艺,解决了这一问题。摩擦焊接是固态连接工艺,没有金属溶解过程,而是靠摩擦热和压力使得金属软化成为可塑状态,进而达到“接合”的目的,这样焊接区材料性质基本没有发生变化。
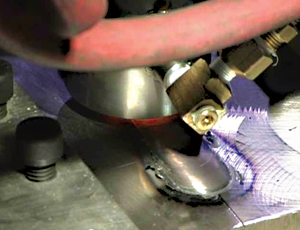
Corrosion-related coiled tubing (CT) failures are costly and significantly impact the safety and reliability of CT operations. CT strings retired at an early stage due to corrosion problems represent an inefficient use of operational assets.
In addition to severe above-ground bending and straightening cycles and bending associated with wellpath curvature, corrosion is also a predominant cause of tubing failure in conventional CT.
Typically, CT is made from high-strength, low-alloy steel. During well servicing and workover operations, exposure of the interior and exterior tubing walls to corrosive downhole environments and treating chemicals can advance the corrosion process. A common early source for corrosion is the welded joints of single strips of tubing.
Galvanic corrosion can occur where a dissimilar metal has been introduced into the tubing string (primarily through plasma arc welding).
A new process known as friction stir welding promises to reduce CT strings’ susceptibility to galvanic corrosion by creating a joint between two strips of parent steel without introducing new dissimilar metal to the string.
Friction stir welding
The process is not new. According to Bob Bunch, president and CEO, Global Tubing, the core technology for friction-stir welding was invented in 1991 by the Welding Institute in Cambridge, UK.
Friction-stir welding is a solid-state joining process; no melting of metal takes place during the bonding process. The technology uses frictional heat and pressure to soften parent steel materials into a plastic state to essentially “stir” them together without the use of filler material.
This process was first used for aluminum and has proven a reliable and valuable tool that is preferred in aerospace engineering. The process was envisioned for harder metals, but due to short bit life, the process was not commercially viable.
In 2004 Megastir, now part of Smith Industries, developed an improved bit for use on friction-welded steel, making the friction-stir welding process commercial. The redesigned bit stemmed from polycrystalline diamond compact technology and is specifically known as PCBN (polycrystalline cubic boron nitride). The development of the PCBN bit provided the technology with an economic potential for use with harder metals, and friction-stir technology has now been adapted to several industries, including vessel construction.
CT innovation
Now that modern friction-stir welding systems employ more robust bits, it is economically feasible to weld high-strength, low-alloy steel. Global Tubing has developed the world’s first coiled tubing manufacturing facility using this new technology.
Conventional arc welded strings are typically de-rated by the systems which measure coiled tubing fatigue due to the presence of the arc weld and this typically reduces the life of CT strings. Friction-stir welding does not have the same negative result. Because the process uses pressure and friction to heat the parent material, no melting takes place. This allows the steel’s grain structure to remain uniform. Without the use of traditional arc welding, property variations across the weldment are greatly reduced.
“In all of our fatigue testing, we’ve seen similar results with solid tubing stressed side by side to a section with a friction stir weld,” Bunch said. Reliability is further improved by the highly mechanized nature of the friction stir weld process. The fully automated process behaves much like a machining process using predictable pressures, rpms, and weld speed and the results are much more repeatable.
With no filler material added to the bias weld, stir-welded tubing is less susceptible to galvanic corrosion — a major problem for traditional plasma-arc-welded tubing strings.
The “stir zone” structure contains no over/under melting of joint corners at the intersection of the joint and strip edge. And because this process results in a refined grain structure, X-ray inspection is improved because gamma-ray diffraction through the material is reduced. In addition, the parent metal thickness is controlled with no post-weld grinding or planishing.
‘Green’ CT technology?
“Friction stir welded tubing is also manufactured with less impact to the environment as well as helping us provide a safer and healthier workplace for our employees.”
Bunch said. Because the strip ends are welded with friction, no fumes are released into the atmosphere (welding fumes normally contain hexavalent chrome, a heavy metal known for polluting the air as well as workspaces). With no arc welding, heavy grinding is also eliminated. According to Bunch, the dust created by arc weld grinding is the number one cause of recordable injuries in tubing manufacturing. In addition, no UV rays are produced from the friction stir welding process so there is no requirement for special safety apparatus.
The overall process of manufacturing tubing with friction stir welding uses less energy than traditional arc welding. As a result, Global Tubing’s facility, located in South Texas near Houston, has effectively decreased its carbon footprint from that of a standard manufacturing facility.
Other technology
Global Tubing’s new facility also uses other technologies new to the coiled tubing market. Weld Scan is an infrared camera developed by Therma-Tool, and is used to record and analyze the seam weld process for the length of tubing. Although this technology is not new technology, this is the first time it has been used for coiled tubing manufacturing. The tool gives an operator the ability to look at a “picture” of the seam weld and adjust welding frequency and other parameters to unsure the highest quality weld. Specially designed to image the weld process through steam and smoke generated during the process, Weld Scan helps the operator determine the parameters of the welding process and to ensure that the integrity of the weld. The end result is a more concise, consistent seam weld, which further improves the overall reliability of the tubing string.
In addition to incorporating a means of viewing the weld, Global Tubing’s facility is also the first of its kind to use a variable frequency ERW seam welding system. With the seam in view, an operator can modify the welding temperature to ensure that welds penetrate the different thicknesses of a tapered string.
Into the field
Global Tubing opened for business in January 2009. To date, the company has manufactured a limited amount of tubing for testing purposes. And it has already shipped its first orders of tubing to the field, although no field results have yet been reported.
Global Tubing holds a provisional patent for use of friction stir weld technology for the manufacture of coiled tubing, with the key patent being sub-licensed to the company. The friction stir welding does not infringe on current bias-weld patents.
杨宝剑 是振威(全球)石油网的高级技术编辑,在石油技术资讯行业有八年的学识和经验。他源源不断地提供石油行业全球最新的技术创新、研发成果、现场应用情况等信息。如果你对该项新技术有任何的疑问,或者对“新技术新产品”未来的内容有任何问题或建议,请联系杨宝剑编辑 +86 10-58236512 Email:
allenyo@zhenweiexpo.com 欢迎与行业互动!