简介:荷兰一家名为Twister BV的超声波气体处理技术公司,最近发布一款新产品。该产品为一新型的气体处理设备,能够促进两相流体的分离,并且能够强化下游分离器的分离效率。Twister SWIRL阀门能够再不关停流体的情况下进行故障检修,减少化学剂的损耗,保证高效采油率。
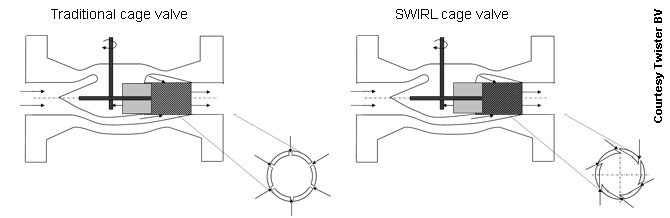
The Netherlands-based Twister BV company recently unveiled a new gas-processing product which promises improved separation of two-phase flow and greater separation efficiency of downstream separators. The Twister SWIRL valve is designed to effectively debottleneck flow problems in existing separator trains while also minimizing liquid carry-over and/or gas carry under, reducing chemical losses, and enabling significantly higher liquid recovery.
The design of many valves currently used in the industry brings about an intense mixing of the gas and liquid phases during the throttling process, which can diminish the efficiency of separators downstream of the choke. The SWIRL valve, by contrast, is a modified choke valve designed to minimize the mixing of gas and liquid phases and enable agglomeration of the dispersion present after pressure let down. The valve uses the available free pressure to create a strong rotational motion in the fluids, resulting in an immediate separation of the formed phases, according to Twister BV.
In conventional valves, flow is throttled over a perforated cylinder, or cage (L). These perforations normally have a radial orientation. The SWIRL valve's modified cage forces the flow into a swirling motion (R).
The rotational motion is initiated by forcing the choking flow through tangential slots in the valve’s trim, which causes small droplets to concentrate along the pipe wall’s perimeter. The ability of the valve to create a regular velocity pattern with less interfacial shear helps ensure that these smaller droplets coalesce into larger drops. The company states that the mean diameter of droplets created through the SWIRL valve is five times larger than that from conventional valves, which improves the efficiency of downstream separators, whose operation is dependent on droplets being larger than a given cut-off diameter.
The company states that the SWIRL principle can be applied to any valve which incorporates axis-symmetrical flow paths such as those developed in cage-piston type valves. Applicable production scenarios for these valves include:
Joule Thomson (JT) expansion of gas flows
Flashing oil/condensate flows in stabilization processes
Oil/water separation
When installed in existing facilities, the new valve technology reportedly offers improved hydrocarbon dew-pointing performance of existing JT-Low Temperature Separator processes, less liquid carry-over and gas carry under, and an overall higher liquid recovery with less loss of chemicals.
Additional details are available on the Twister BV website.