简介:随钻测井(LWD)以及旋转操控技术越来越难以在极端作业环境下实施,这些精确的钻井工具需要在钻井作业过程中能承受长达数日的高温环境,这对其来说是一个考验。针对这种情况,哈里伯顿经过努力开发出能够承受高温高压的高强度钻进测量系统。该系统能够承受高达175°C,压力达到30,000 psi。系统由传感器组成。是哈利伯顿和道达尔合作完成。
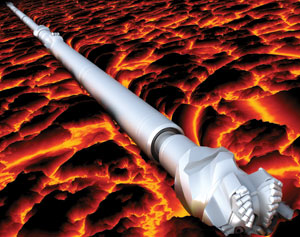
Logging-while-drilling (LWD) and rotary steerable technologies have traditionally been very difficult to deploy in hostile environments, because sophisticated tools are exposed to extreme heat downhole during the entire drilling operation that may go on for days.
Exhaustive engineering analysis and rigorous testing and development have resulted in Halliburton introducing a plethora of systems with significantly higher tolerance for high-pressure/ high-temperature (HP/HT) conditions. The company’s HP/HT point the-bit rotary steerable system is ruggedized to withstand temperatures as high as 347°F (175°C) and pressures to 30,000 psi; with survival temperatures up to 392°F (200°C). Complementing the HP/HT drilling system is the suite of measurement-while-drilling (MWD)/LWD sensors rated to 347°F (175°C) and 25,000 psi. These sensors have been proven in nearly 600 HT runs and more than 35,000 ft (10,675 m) of HP hole last year alone.
Last year TOTAL chose to enter into an agreement with Halliburton to jointly develop a suite of ultra-HP/HT measurement and LWD sensors. In collaboration with TOTAL, Halliburton is now developing the Prometheus suite of LWD tools specifically for the ultra- HP/HT environment of some North Sea fields, where harsh conditions challenge the limits of current technology.
In rigorous testing to ensure operational reliability, Halliburton subjects all existing
HP/HT tools to a specific temperature profile, which includes operational tests at 347°F (175°C) and non-operational soaking at 392°F (200°C). The Prometheus suite, however, will have to surpass even these current capabilities.
Extreme proving ground
Halliburton’s HP/HT technology was recently put to the test when the company’s HP/HT rotary steerable system (RSS) was run on a HT field appraisal campaign in the central sector of the UK North Sea.
For this extreme drilling environment, the HP/HT RSS was combined with an HP/HT quad-combo LWD suite comprised of an azimuthal lithodensity sensor, compensated thermal neutron sensor, resistivity sensor, and bimodal acoustic sensor.
Built and delivered specifically for the challenges of drilling this operator’s HT wells, the HP/HT RSS and LWD sensor combination performed flawlessly, experiencing real-time temperatures of 305°F (152°C) and recorded temperatures approaching 320°F (160°C).
Use of the proprietary downlinking software enabled surveying with the pumps on, which provided considerable benefit when staging circulation for mud cooling. This process typically would take more than five minutes at connections, wasting precious offshore rig time. In addition, to ensure the safety and efficiency of the HP/HT operation,
Halliburton’s drilling optimization service specialists provided 24-hour well monitoring of connection flow, equivalent circulating density, and hydraulics management. They also detailed vibration monitoring, which is essential for maintaining downhole tool reliability in HT environments.
Using the customized combination of Halliburton HP/HT technologies, the customer realized an immediate 24% increase in penetration rate when compared to motordrilled offset wells.
In addition to faster penetration rates, precise wellbore placement, and improved hole quality, the use of HP/HT system technology allowed for real-time reservoir evaluation while-drilling which, in turn, streamlined subsequent wireline logging runs, resulting in significant cost reduction and rig time savings.
Another example of an integrated HP/HT solution delivered by Halliburton is a recent job in the central North Sea.An operator was seeking faster rates of penetration through an HP/HT hard chalk sequence of their well. Halliburton deployed a motor-driven RSS for HT environments paired with an HP/HT LWD quad combo.
The HP/HT motor-driven RSS was particularly suited to the hard, HT formation, as it can deliver unmatched endurance under the most hostile of drilling conditions, helping to improve instantaneous and average rates of penetration, reduce trips, and ensure precise wellbore placement in all drilling environments.
The HT RSS with an enhanced performance motor delivered penetration rates an estimated 33% higher than with a conventional rotary system. Drilling optimization was the key to achieving these results: using Sperry’s innovative directional drilling monitoring software, the process was “modeled, measured, and optimized” in real time.
The LWD technology also performed flawlessly under the harsh conditions and delivered what is now the hottest ever HP/HT quad combo run in the North Sea with downhole temperature reaching greater than 175°C (347°F). The HP/HT LWD combo consisted of a compensated thermal neutron sensor, azimuthal lithodensity sensor, slimhole resistivity sensor, pressure while-drilling wellbore pressure measurement sensor, directional module, and bi-modal acoustic sensor. All sensors provided 100% data to the point of thermal shutdown. LWD data availability reduced the length of wireline run and enabled the operator to optimize their completion strategy, more accurately determining perforation intervals and improving production estimates.
Development of the Prometheus suite is expected to extend these benefits to even more extreme drilling environments, allowing more cost-effective exploitation of hard to-reach reservoirs.
Prometheus suite
Prometheus suite of ultra- HP/HTM/LWD tools is being developed for TOTAL’s Victoria field in the North Sea.
Scheduled to begin in late 2010, “Project Victoria” will require Prometheus tools to be rated to 230°C (446°F) and 30,000 psi. First to be developed are directional probe, pressure-while-drilling sensor, and gamma ray sensor. Halliburton is aiming at achieving tool survivability at 250ºC (482°F) for the length of a 14-day bit run. The tools will be available for 57⁄8 in. up to 97⁄8 in. hole sizes.
With no existing technology capable of allowing LWD/MWD electronics to survive in such extreme temperatures, Halliburton scientists and engineers are already evaluating several ways to address this challenge using innovative, industry first concepts including a downhole refrigeration system, cold plate technology, and flasking.
The cold plate is a metal plate near which the electronics can be mounted, which can quickly carry the heat away from the processors. A similar technology is used in personal computers.
“Flasking” means putting the electronics inside a special chamber, which can be filled with a low-density gas or a vacuum, reducing heat transfer from the environment to the electronics. It delays the amount of time it takes for the environmental temperature to reach the electronics. Flasking is not something new?it’s been used in the wireline industry for a long time?so that wireline tools can run electrical components that are rated to a relatively low temperature in a HT well.
For refrigeration, Halliburton will experiment with using a downhole turbine, which will generate electricity from the flow of the drilling fluid. The electricity will be used to power a refrigeration unit. It will likely use phase change technology (similar to a domestic refrigerator).A special liquid is allowed to expand, causing it to evaporate and get colder, cooling the environment around it.
If Halliburton successfully manages to make drilling and formation evaluation work at these extreme temperatures, it could open up access to many more oil fields around the world.
杨宝剑 是振威(全球)石油网的高级技术编辑,在石油技术资讯行业有八年的学识和经验。他源源不断地提供石油行业全球最新的技术创新、研发成果、现场应用情况等信息。如果你对“新技术新产品”的内容有任何问题或建议,请联系杨宝剑编辑 +86 10-58236512 Email:
allenyo@zhenweiexpo.com 欢迎您提供手中的最新技术文章!