简介:水平井完井的经济型方法是利用诸如DirectStim 系统进行快速完井。多层水平井完井技术能够采出更多产能。BJ油服公司建议使用OptiFrac SJ 连续管输送沙砾喷嘴进行套管射孔技术,以及用LitePlug 砂堵来稳妥地替代脆弱桥塞技术。
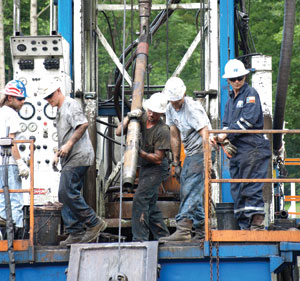
One way to improve the economics of horizontal fracturing is with time-saving completion systems such as the DirectStim system, shown here being run into a well in West Virginia. (Images courtesy of BJ Services)
Economics have driven the development of new technologies aimed at drilling, completing, and stimulating horizontal wells. Horizontal wells are interesting because they allow access to long reservoir segments from a single surface portal, thus minimizing drilling costs, surface infrastructure requirements, and surface environmental impacts.
However, completing and stimulating long horizontal wells is typically done in multiple stages, requiring more stimulation treatments than would be economical for vertical wells. The practice provides earlier access to reserves and faster returns on the drilling investment but increases fluid and proppant requirements and completion time.
To maintain economics and environmental stewardship for these multizone horizontal wells, operators look for ways to minimize the cost and ecological impact of zonal isolation and stimulation ? without affecting production or safety.
Staged treatments
In northeast British Columbia, for example, an operator commonly drills several wells from one pad to produce from a tight gas formation. Typical wells are 7,900 ft (2,400 m) total vertical depth and 15,700 ft (4,800 m) measured depth with complex horizontal trajectories. Typical bottomhole pressure and temperature are 4,641 psi (32 MPa) and 200°F (95°C), respectively. Early field development consisted of traditional plug-and-perf stimulation, which was proving uneconomic in the field. In particular, mis-runs and premature plug setting cost the operator more than US $500,000 (per interval) to get back on track due to time and services involved in milling, clean-outs, re-perforation, etc.
BJ Services engineers suggested a pair of technologies that promised enormous savings: OptiFrac SJ CT-conveyed sand jetting nozzle to perforate the casing, and LitePlug sand plugs that would reliably replace the finicky bridge plugs.
Sand-jet perforating offers two advantages. First, it eliminates the non-productive time (NPT) required for the traditional multiple trips of shaped-charge perforating because the coiled tubing (CT) can move up-hole to the next target zone while the frac crew is stimulating the just-perforated zone. Second, abrasive perforation minimizes near-wellbore damage compared with conventional technology.
The LitePlug technology combines conventional sand and LiteProp proppants to create consolidated sand plugs that provide zonal isolation even in horizontal wells.
After all the zones are completed, the LitePlug material can be cleaned out of the well quickly using CT nozzles, eliminating the NPT required to set and mill conventional bridge plugs. One customer estimated the technologies saved $450,000 per well compared with traditional plug-and-perf stimulation. Since their inception, the technologies have been used together to stimulate some 360 multizone wells in the US, Canada, and South America.
Sliding sleeves
Sliding sleeve technology, such as the DirectStim system, provides another time-saving alternative for multizone completion. Run in with the production tubing, this system uses hydraulically actuated openhole packers to isolate each horizontal zone and frac sleeves to allow access. At the end of each zone’s stimulation treatment, a ball is dropped to isolate that zone and open the next zone’s frac sleeve. The technology can be used in conjunction with common stimulation technologies, including traditional fracs and more recent techniques that further improve horizontal well economics. Typically used in openhole completions, the technology eliminates some well construction costs as well as tripping time for traditional plug-and-perf stimulation operations. As a result, the technology has been popular for completions and stimulations in the US and Canada.
Improving frac economics
Another technique has been used to save money while optimally stimulating horizontal wells in the Wolfcamp formation in Eddy County, NM. Typical stimulations before March 2006 were four-stage traditional fracture treatments using 4% to 9% CO2 with a slick freshwater fluid system placing 100-mesh Ottawa and 20/40-mesh Brady sand at 0.2 to 0.8 and 0.4 to 1.2 lb/gal, respectively.
To improve the economics of the treatments, BJ Services pumped a series of 24 stimulation treatments using a lower concentration of ultra-lightweight proppant as a partial proppant monolayer in the fracture. Although the cost per pound of proppant was higher, the partial monolayer designs required much less proppant to achieve optimal fracture conductivity and geometry.
Whereas conventional sand fracs used several hundred thousand pounds of proppant, the partial monolayer fracs required about an order of magnitude less, resulting in an overall average stimulation cost savings of 19.3%. In addition, the wells treated using partial monolayer designs had comparable or better production results, with 2.2% slower declines and therefore higher 12-month cumulative production compared to regular sand fracs.
Although it is tempting to compare costs of individual components of a fracture stimulation plan, it is particularly important when using new technologies to consider the total return on fracturing investment. The superior conductivity benefits of partial proppant monolayers have been theorized since the 1950s, but they were difficult to achieve in practice until after ultra-lightweight proppants were commercialized. Since then, the technologies have been proven effective in thousands of wells, horizontal and vertical, around the world.
Better nitrogen fracs
In another example, in the Big Sandy field of the eastern US, some 25,000 wells produce gas from Berea tight gas sands and Devonian Ohio shales. The low-pressure reservoirs are considered fluid-sensitive and have traditionally been stimulated with high-velocity nitrogen or nitrogen foam treatments, with or without proppant. As with the New Mexico wells, field experience had determined strong economic benefits from using ultra-lightweight proppants instead of conventional sand.
In early 2008, an operator performed field trials of a new technology made possible by the ultra-low density (1.06 sg) of the ultra-lightweight proppant. To enable the proprietary VaporFrac services, the proppant is pre-slurried in a small amount of non-damaging slickwater fluid and injected directly into a high-pressure nitrogen gas stream as it is pumped downhole. The resulting fracturing fluid comprised of 94% to 98% nitrogen, greatly reducing the fluid sensitivity concerns. Post-frac cleanup, water disposal costs, and proppant flowback are virtually eliminated. Treatment costs and environmental impact are reduced relative to conventional approaches.
The operations are designed to achieve partial monolayers of proppant to maximize fracture conductivity. Vertical trial wells achieved 88% to 250% higher 30-day cumulative production than 15 comparable offsets. The degree of success encouraged the operator to proceed with trials in horizontal wells averaging eight intervals each. A technical discussion of the horizontal well designs and significant production improvements will be presented at the 2009 SPE Annual Technical Conference and Exhibition in New Orleans, La., Oct. 4-7.
Environmental impacts
The key feature of ultra-lightweight proppants is their nearly neutral buoyancy in slickwater systems, providing for minimized settling when trying to pump proppant far out into horizontal well sections. This can save money on frac fluids, minimize the potential for formation damage, and provide environmental benefits in terms of simplified reuse and recycling. For areas where reservoir properties preclude the use of ultra-lightweight proppants and to further reduce freshwater requirements for stimulation, other environmental solutions have been developed.
The issue of frac fluid use and reuse has come to the fore as horizontal drilling has enabled economic oil and gas development in areas where water is scarce. As development has increased in unconventional reservoirs ? the Barnett, Marcellus, and Bakken shales, for example ? environmental pressures have encouraged operators to seek alternatives to using and then properly disposing of the millions of barrels of fresh water required to drill and stimulate each well.
Versatile technologies such as BJ’s Viking II PW (produced water) and AquaStar fluids allow reuse of stimulation flowback or produced formation water. Field experience in the Marcellus shale in 2008 determined that produced water from coalbed methane fields can also be used to reduce the freshwater requirements of stimulation treatments in that area without adversely affecting gas production. Such solutions can provide economic benefits as well as environmental ones: A customer in the Bakken shale estimated that recycling frac fluid and produced water saved 10% to 15% of total stimulation cost because of reductions related to hauling, heating, and disposing of fluids and other related costs.
杨宝剑 是振威(全球)石油网的高级技术编辑,在石油技术资讯行业有八年的学识和经验。他源源不断地提供石油行业全球最新的技术创新、研发成果、现场应用情况等信息。如果你对“新技术新产品”的内容有任何问题或建议,请联系杨宝剑编辑 +86 10-58236512 Email:allenyo@zhenweiexpo.com 欢迎您提供手中的最新技术文章!