作者
顾望平
国家压力容器与管道安全工程技术研究中心
(合肥通用机械研究院)
我国炼油厂行业的现状:
#原料劣质化趋势严重
#部分装置原设计不能满足原料劣质化要求
#部分重点装置材质升级不彻底
#装置长周期安全运转的要求
#设计与建设遗留问题多
#管理粗放
#缺乏技术支持
#人员变动大
因腐蚀非计划停工
随着原油性质不断劣质化,因腐蚀引起的装置非计划停工一度成为非计划停工的主要原因。
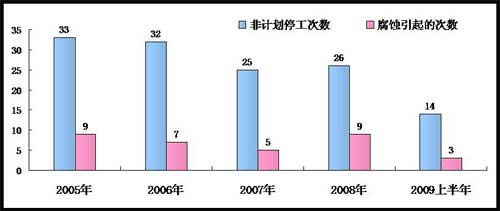
腐蚀介质来源
原油:氯化盐、硫化物、有机酸、氧、氮化物,有机氯化物,重金属等;
运输和生产中加入的助剂:氯化物、酸、碱、氢氰酸、糠醛、胺等;
炼制过程生成的:硫化氢、二氧化碳、氰化物、氢、盐酸、氨、氯化氨、有机酸、连多硫酸、二硫化物、酚等;
这些腐蚀介质在工艺环境下腐蚀金属材料归属不同的腐蚀机理,
有机氯腐蚀的防止
注碱可以将氯化镁转化为氯化钠热稳定盐。但注碱也会给二次加工过程带来一些不利影响。日本炼油厂的工艺防腐技术在电脱盐罐前、常压炉前和常压塔顶少量注碱(4ppm),有很好的效果。
目前国外一些停止注碱多年的炼油厂又重新对注碱产生兴趣,为了避免注碱的不利方面,需要严格控制碱的注入量、浓度并改进加注方法。
镇海分公司在电脱盐后的原油管线注入碱液NaOH=4%wt , 1617 mL/s, 注入量为2.5g/吨油。结果表明, 常压塔塔顶换热器腐蚀速率下降约80% ,常压塔塔顶回流罐污水中Cl- 浓度至少下降80% ,常压塔塔顶回流罐污水pH值维持在6. 0~7. 5,中和剂消耗量也由注碱前的150~180 kg/d 降低至注碱后的100~120 kg/d,且注碱操作不会影响常减压装置工艺运行的稳定和二次加工装置的原料质量。
炼制工艺中发现的腐蚀剂
硫 存在于原油中。它引起金属的高温硫化,并与其他元素结合在一起形成侵蚀性成分,如硫化物、硫酸盐、亚硫酸、连多硫酸、硫酸。
环烷酸 有机酸的集合名称,主要在我国渤海湾、齐鲁和中国西部,某些国外的进口含酸油发现它们的存在。
连多硫酸 当设备停用时,由于硫化物、水分和氧的相互作用而形成的亚硫酸。
氯化物 以盐的形式存在,如氯化镁和氯化钙,它们来自原油、催化剂、冷却水。对不锈钢有应力腐蚀开裂与点蚀。
二氧化碳 在制氢装置中,烃的水蒸汽转化过程会产生二氧化碳,并且,在催化裂化中也产生一定的量。二氧化碳与水分结合在一起形成碳酸,腐蚀碳钢设备。
氨 进料中的氮与氢结合生成氨(或者氨被用于中和),然后,它与其他元素结合形成腐蚀性成分,如氯化铵。
氰化物 通常在高氮进料的裂解时会产生氰化物。存在氰化物时,容易加快腐蚀速率。
氯化氢 通过氯化镁和氯化钙的水解而形成氯化氢,许多塔顶(蒸汽)流体中可以发现它们的存在。在冷凝时,它形成高度侵蚀性盐酸。
硫化氢 存在于含硫原油和天然气中。是有机硫化合物分解或者与某些加工装置中的氢反应而生成的。
氢氟酸 在烷基化装置中用作催化剂,氢氟酸腐蚀经常伴有氢致开裂产生 。
硫酸 在烷基化装置中用作催化剂,并且在含有三氧化硫、水、氧的某些工艺流体中会生成硫酸
更多内容,参见资料下载频道
石化厂常见的腐蚀失效与对策。